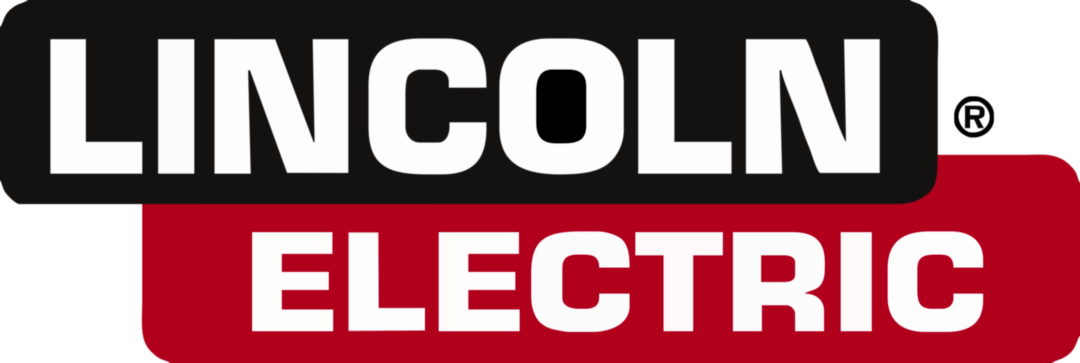
Controls Engineer
Lincoln Electric
- Fort Loramie, OH
- Permanent
- Full-time
Employment Status: Salary Full-Time
Function: Engineering
Req ID: 24515Candidate may reside anywhere in the US and travel would be required.PURPOSE: Controls Engineering design position for the design, implementation and troubleshooting of customer tooling and equipment.JOB DESCRIPTION (DUTIES AND RESPONSIBILITIES):
- Provide support to the Applications Engineering Dept. for estimating labor and materials.
- Visit customer site for purposes of gathering information, project kickoffs or project reviews.
- Visit customer site to troubleshoot, repair or implement systems.
- Attend Project Kick Off meetings, to gather important project scope details.
- Concept and design equipment according to a blending of Customer Build Specifications, Customer RFQs, Lincoln Quote, process requirements, and industry safety standards
- Create electrical controls schematics including wiring diagrams, panel layouts, push-button station layouts, safety circuits, pneumatic layouts and other hardware related documents.
- Develop and place requisition for all controls associated material/parts related to a project.
- Organize, produce, correct and manage schematic hardcopies throughout the production of the equipment.
- Regularly schedule and attend general project-based meetings.
- Communicate internally & externally to resolve project concerns, via phone, e-mail and web-conferencing.
- Manage the quality, timing, and scope of equipment provided by external suppliers.
- Collaborate with other departments to develop solutions.
- Monitor and maintain quoted material and labor budget.
- Proactively alert project team members when the material or labor budget is impractical or likely to be exceeded.
- Lead, direct and manage internal and/or external resources during situations requiring workload distribution.
- Trouble shoot wiring problems and circuit issues.
- Provide support to the assembly department by answering questions and addressing issues.
- Provide documentation to the programming department, such as I/O addressing, machine sequence, and bring attention to special/unusual/ high-end components.
- Participate in quality audits of equipment.
- Work with vendors and manufacturers on cost, deliveries, cross-referencing and application solutions.
- Research and develop circuit designs for new technology, components and processes.
- Participate in company or department wide improvement initiatives.
- Participate in the development of innovations.
- Participate in the development and management of department processes, such as CAD library & functionality, operating procedures, software tools and design methods.
- Understand and comply with established ISO9001 processes and procedures specific to the Controls Department.
- QPP-04.01, Section H
- WI-42
- WI-43
- Maintain up to date training on ever changing Safety and Industry build standards.
- Stay current with compliance training modules required by Lincoln.
- Fill in for Controls Department Manager during extended periods of time off, by assigning kick off invites, managing issues and delegating resources.
- Bachelor’s degree in electrical engineering or equivalent experience
- 5+ years of Controls Design experience
- Strong AutoCAD Electrical Skills
- Comprehensive knowledge of industry safety design standards and best practices
- NFPA 79
- NFPA 70E
- ANSI/RIA
- ISO 12100 & 13849
- Good computer proficiency in Microsoft office applications
- Experience with Allen Bradley, Siemens and Omron PLC’s and HMI’s.
- Experience with Fanuc, ABB and Yaskawa robots.
- Design Experience with Allen Bradley PLC's and HMI's
- A wide-ranging knowledge of AC/DC power, motors, drives/motion control, industrial controls, pneumatic valves and sensors.
- Experience in industrial networking & various communication protocols.
- Experience with robotic welding (arc, laser, resistance)
- Experience with commonly used concepts, practices, and procedures in machine control design.
- Experience with manufacturing and tooling processes.
- Recognized as highly competent in own area within the organization.
- Has sufficient depth and/or breadth of expertise in own discipline or function.
- Interprets internal or external issues and recommends solutions/best practices.
- Solves complex problems; takes a broad perspective to identify solutions.
- Works independently, receives minimal guidance.
- Often Leads functional teams or projects with dependable track record.
- High level of efficiency, attention to detail and organizational skills
- Dependable leadership, communication and relational skills
- Proven industrial electrical design experience and troubleshooting electrical circuitry.
- Excellent knowledge of LEA equipment build standards and the QA ISO 9001 program including: QPP-04.01, Section H, Work Instructions WI-42 and WI-43
- Exhibits flexibility and adaptability in handling change
- Ability to manage multiple projects and priorities reliably.
- Relies on experience & judgement to plan, make decisions and accomplish goals.
- Physical demands: While performing duties of job, employee is occasionally required to stand; walk; sit; use hands to finger, handle, or feel objects, tools, or controls; reach with hands and arms; talk and hear. Specific vision abilities required by the job include close vision, distance vision, color vision, peripheral vision, depth perception, and the ability to adjust focus. Repetition with activity; computer work.
- Work environment: The noise level in the work environment is usually moderate.