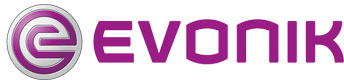
Changeover Project Lead
Evonik
- Lafayette, IN
- Permanent
- Full-time
- Bachelor’s Degree in engineering preferred and at least 10 years project execution and plant experience.
- Project Management Certifications preferred.
- Strong communication and organizational skills with emphasis on oral and written communication
- Strong computer skills in a variety of software packages (MS Office, SAP) Ability to influence groups without having direct supervisory responsibility.
- Ability to cope with the stress of working on several projects concurrently and dealing with critical deadlines.
- Demonstrated ability to provide tactical leadership of a group to achieve a common objective with a broad range of impact.
- Some supervisory experience desired (including coaching employees to improve performance).
- Strong, demonstrated knowledge of manufacturing business processes.
- Demonstrated ability to motivate and mentor others in a manufacturing environment.
- Ability to identify and improve business processes by analyzing data, developing countermeasures, implementing action plans, and monitoring results.
- Ability to communicate clearly and effectively across all levels of the organization.
- Flexibility in hours is required as the role supports a manufacturing plant that operates 24/7/365.
- Occasional travel may be involved.