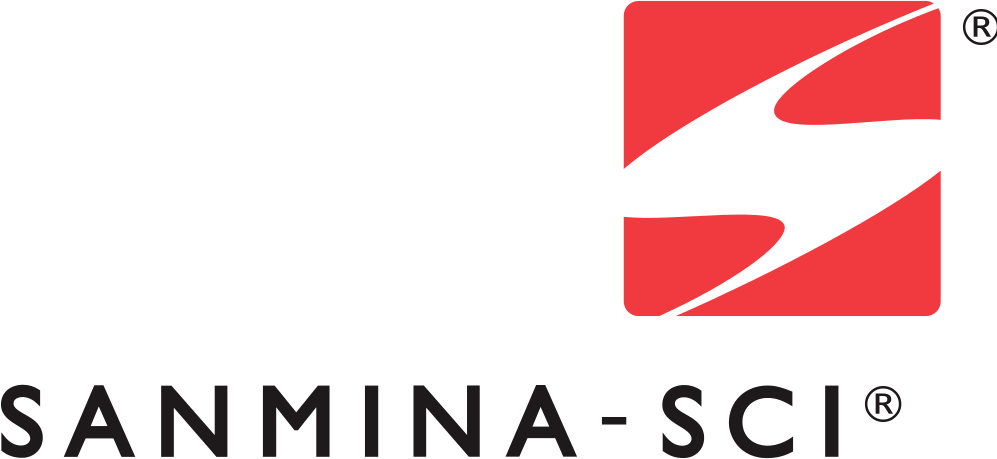
Planning Manager
Sanmina
- Manchester, NH
- Permanent
- Full-time
Oversees activities related to the purchase of material, material control, inventory control, shipping/receiving and stores
functions. Manages the activities of the team and is responsible for staffing decisions, training and development, and
performance management of the staff. Develops, implements, and maintains policies, procedures and material control
systems. Ensures materials are ordered and in stock to meet company requirements, while maintaining acceptable
inventory levels. Develops material schedules and coordinates the efficient movement of materials with purchasing,
production and engineering. Reviews and plans requirements for purchasing materials. May prepare material
requirement plans using enterprise resource planning systems. May assist with the establishment and maintenance of
the production control system. Selects, develops, and evaluates personnel to ensure the efficient operation of the
function.ESSENTIAL JOB DUTIES
- Key focus is on leadership and motivation of staff, and contributing advanced Supply Chain, Planning and Purchasing expertise.
- Receives assignments in the form of objectives and establishes goals to meet objectives.
- Provides guidance to subordinates to achieve goals in accordance with established policies.
- Work is reviewed and measured based on meeting objectives and schedules.
- Establishes and recommends changes to policies which effect immediate organization(s).
- Works on issues of diverse scope where analysis of situation or data requires evaluation of a variety of factors,
- including an understanding of current business trends.
- Follows processes and operational policies in selecting methods and techniques for obtaining solutions.
- Acts as advisor to subordinate(s) to meet schedules and/or resolve technical problems.
- Develops and administers schedules and performance requirements.
- Responsible for all Planning & Purchasing functions to ensure that the group's objectives and processes align
- with the overall business direction; supports employees to achieve their objectives, and removes barriers to
- success.
- Works with employees to plan, assign, and monitor individual objectives and activities based on overall group
- priorities, and company strategy. Provides useful and timely feedback to staff members on their performance
- and development plan. Takes the lead on difficult employee situations.
- Responsible for defining and establishing Supply Chain, Planning, and Purchasing programs and processes that
- optimize company effectiveness. Oversees all Supply Chain, Planning and Purchasing functions, and is
- responsible to ensure compliance with relevant company policies and procedures, legislation and industry
- standards.
- Effectively liaises with suppliers to ensure strategies, programs and processes required to meet business goals
- and objectives are implemented and performance is monitored. Ensures corrective actions plans are
- documented and instituted quickly for all performance levels under standard.
- Provides various complex reports, analyses, and recommendations as defined by management, both on a
- regular and ad hoc basis.
- Manages deliverables agreed to for the group overall, providing management with regular updates, identifying
- issues, and barriers, and solutions.
- Has full and in-depth knowledge of VMI and works with teams from both the vendor and internally to ensure
- that manufacturing and demand are synchronized.
- Responsible for site Excess and Obsolete (E&O) and reduce finance impacts
- Responsible for material cost analysis such as MCPU (material cost per units) review and provide the
- management inputs regularly.
- Minimum 5 years manufacturing experience, preferably in a fabrication or metal
- BS degree or higher preferred in Manufacturing Management or other related discipline.
- Direct shop floor supervisory experience a plus
- Excellent verbal and written communication skills essential.
- Successful experience in a fast paced, multitasking environment required.
- Microsoft Office, and/or advanced Excel skills a plus