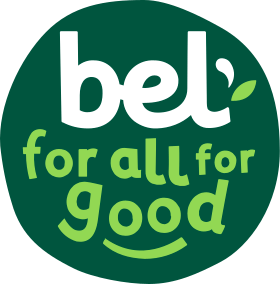
Industrial Performance Engineer
Groupe Bel
- Nampa, ID
- Permanent
- Full-time
- Ensure the development, implementation and sustainability of industrial standards and plant processes as assigned by the Industrial Performance Manager.
- Areas of influence and responsibility may include: industrial procedures, training and qualification standards, maintenance and operational excellence standards (Root Cause Analysis, 6S, Daily Accountability, VPA, Lean Manufacturing principles) and Environmental, Health, Safety and Quality.
- Seek to identify best practices from other internal plants and plants external to Materne that can be integrated to our plant.
- Ensure that improvements and lessons learned are shared with the rest of the organization to enhance standardization and increase performance company-wide.
- Lead or participate in continuous improvement projects or task forces, and deliver measureable, sustainable results.
- Develop plant employees relative to root cause analysis, continuous improvement principles and methodologies, 5S, etc. thru developing and delivering training, coaching, and mentoring.
- Uses DMAIC methodology: define, measure, analyze, improve, and control the results
- B.S. degree in a Technical Field or at least 5 years of manufacturing experience preferred.
- 5+ years of manufacturing experience with at least 2 years participating or leading continuous improvement initiatives.
- Six Sigma Green Belt (or related certification) is preferred.
- Experience in implementing Lean Manufacturing concepts is preferred.
- Prior food manufacturing experience is highly preferred.
- Must have completed successful DMAIC / Lean projects in production, quality, or supply chain.
- Must have strong leadership skills and be able to lead through influence.
- Must be able to prioritize work.
- Must be able to adapt to a rapidly changing environment.
- Must be able to quickly and effectively interpret information in order to reach sound conclusions.
- Must be able to challenge the status quo in a professional manner.
- Must have a passion for being on the plant floor and interacting with employees at all levels.
- Must have solid written and verbal communication skills.
- Competency with Microsoft office suite is required.
- Competency with data collection and analysis as well as good lab notebook practices are also required.
- Must be able to work a minimum of 8 hours per day
- Must be able lift up to 40 lbs.
- Must be able to travel via airplane within the US and Internationally.