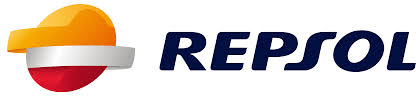
Mechanic
Repsol
- Three Rivers, TX
- Permanent
- Full-time
- Ensure all activities are performed safely, within relevant regulatory and company requirements, and in accordance with HSE standards.
- Carry out planned and corrective maintenance activities on surface equipment as needed and/or scheduled. Ensure that harm is minimized and/or mitigated to personnel, the environment, and the associated equipment.
- Maintain the reliability, availability, and operational condition of Rotating & Reciprocating surface equipment so that production targets can be achieved. Minimize equipment downtime and impacts to production operations.
- Minimize impacts to the production process during equipment maintenance; safeguard the availability & operating condition of all equipment so that production targets can be achieved.
- Assist in maintaining & establishing adequate levels of supplies and designated “critical” spare parts at the appropriate facilities (company warehouses versus vendor storage).
- Receive written, diagrammatic, and/or verbal instructions and determines appropriate actions for all work performed. Prepares written work orders for other personnel to complete repair, maintenance, installation and testing tasks.
- Determine causes of defective performance and reports findings to supervisor. Repairs where appropriate, informs supervisor of repairs requiring a higher level of expertise.
- Repair or Replace Faulty Equipment or individual components such as relays, switches, motors, printed circuit boards,position sensing devices, seals bearings shafts, etc.
- Maintain records of repairs, calibrations and tests by entering data into handwritten logs or computer databases, where applicable. This include safety & regulatory requirements.
- Maintain current technical knowledge of government & company policies, codes & regulations.
- Interpret readings of meters, gauges, pumps, compressors, instrument readings and charts to determine operational capabilities and/or issues.
- Participate in all safety training and assist in safety procedures such as first aid, CPR, fire drills and emergency evacuation.
- Support operational Excellence Program (HSE, mechanical, operational, or clerical),Use Synergy to track and completed actions & identifying opportunities to achieve continuous improvement in their area of responsibility. Relay those ideas to their management team for review and possible adoption.
- Ensure required testing and/or re-calibration of “safety-critical” equipment is performed satisfactorily and on schedule.
- Ensure the use of Repsol’s policies, procedures, and processes when applicable. These include, but are not limited to: E-Permit to work, Safe Job Analysis, Lockout/Tag Out, confined space entry, etc. If qualified, approve work permits according to permit-to-work procedures.
- Become familiar with all mechanical maintenance procedures and work instructions in order to provide cross-functional support as needed.
- Assist the commissioning team during start-up operations of new facilities as necessary.
- Work within the asset to achieve a multi-discipline approach to problem solving and to meet or exceed asset objectives. Communicate with other team members to optimize day-to-day operational activities.
- Prepare reports and generate detailed records and handover notes as required to facilitate proper communications.
- Ensure resources (people, tools, equipment, etc.) are utilized in the safest, most-efficient methods possible.
- Enter Updated Maintenance data in appropriate software (SAP)
- Communicate directly with production and Planning / Scheduling department to coordinate maintenance and repair work to meet maintenance KPI target objectives.
- Participate in safety, health, and environmental programs
- Enforce culture that will stop unsafe work, and correct unsafe work practices
- Manage and Monitor all repair work requests for routine and major maintenance of Maintenance related activities for production & plant operations within a CMMS (SAP) also scheduling, maintenance, executing work orders, reporting, checking system to make sure they are completed.
- Demonstrate ability to make quick, educated decisions based on accurate information.
- Ensure management of change requirements are current with company policy
- Oversee and schedule the work of contract mechanics.
- Fully authorized to work for any employer in the US without sponsorship now or in the future.
- High school degree, or equivalent, in combination with required experience listed below.
- Willing to work overtime, weekends, holidays, and respond to call outs as needed to fulfill business objectives and the ability to work abnormal work shifts to meet plant conditions.
- Preferred: Experience with Ariel, Kaeser, Sullair, Champion, Emax Compressors & prior experience working on pumps would be an asset.
- As the ideal candidate, you would have been a journeyman in the Millwright or Mechanic Field with a working knowledge of both with a minimum 3 years related experience preferably experience in the Oil & Gas or petrochemical industry in a working supervisory role.
- Other combinations of education and experience may be considered.
- Must be proficient in the use of all Microsoft Office software modules, including Word, Excel, PowerPoint MS Office software and SAP others.
- Troubleshoot and repair of rotating & reciprocating equipment and other plant related equipment.
- Knowledge and understanding of ANSI, & API standards and specifications for pneumatic pressure and liquid controllers, throttle/snap pilots, control valves, liquid level switch’s regulators, dump valves,
- Troubleshoot, maintain, and repair Pumps & Compressor systems, and auxiliary equipment including generators.
- Ability to work under DOT, OQ and PSM regulation.
- Install repair and maintain Motors, Engines, Pumps, Compressors, and generators, Knowledge of circuits, wiring and other electrical system equipment and associated components in compliance with Manufacturers Specifications standards.
- Diagnose malfunctioning systems and components using test equipment and hand tools to locate the cause of a breakdown and correct the problem.
- Actively participate in RCA’s and improvement of facility’s Process’s & PM’s
- Basic knowledge of Fluid Mechanics: Pressure, Level, Flow, Temperature & Level parameters, measurement
- Basic knowledge of Surface Equipment Design, Operation and maintenance of Wellhead and Downhole, Artificial Lift, Separation Equipment, Central Facilities, Compressors Generators control systems and Pipeline, Process & Instrumentation Diagrams (P&IDs)
- Hazard Recognition and reporting for risks associated with Well-Site & Production Facilities
- Highly organized with the ability to handle multiple tasks & prioritize work.
- Knowledge of facility’s operation systems able to perform maintenance and repairs to transmitters, control valves and calibration of analyzers and equipment control components.
- Demonstrates corporate values: Safety, Passion, Bias for Results, Respect, Excellence, Teamwork, Honest Communication
- Desire to learn, understand and practice Repsol USA’s safe operations policies and procedures.
- A history of working with practices that emphasize health, safety and environmental protection.
- Experience servicing & trouble shootings reciprocating, multi stage compressors, Pumps.
- Strong project management and scheduling skills as well as the ability to prioritize.
- Ability to effectively guide the work of others
- Excellent communication skills, both written and verbal
- Ability to learn quickly and apply learnings effectively
- Mentor others willingly when capable. Maintenance technicians Apprentices
- Ability to coordinate resolution to sometimes complex issues
- Ability to work effectively under tight deadlines
- Works well independently and with minimal supervision
- The employee may be exposed to a wide range of temperatures depending on weather.
- The noise level is usually loud in some areas including enclosed compressor Stations, Generator, Compressor Packages.
- While performing the duties of this job, the employee is regularly required to stand, use hands, and reach with hands and arms.
- The employee is required to walk, stoop, kneel, crouch, or crawl. The employee may be required to sometimes sit, climb or balance and work at heights..
- Twenty-four hour on- call responsibilities are required
- Ability to lift up to 50 lbs with manual dexterity to lift, bend and jump.
- The employee is occasionally exposed to fumes or airborne particles.